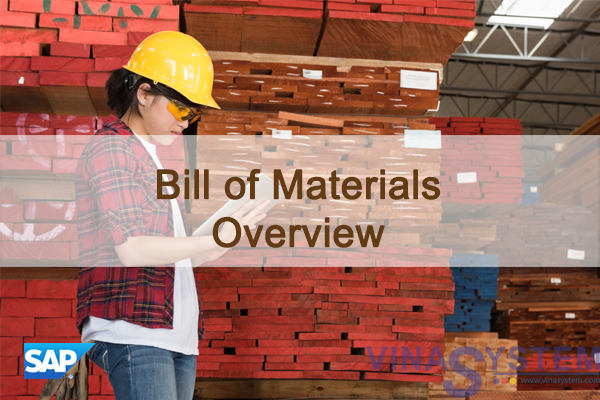
Tổng quan định mức nguyên vật liệu (BOM) trong SAP Business One - Bill of Material
At the end of this topic, you will be able to:
- Describe the Bill of Materials structure
- Describe when to use the different types of Bill of Materials
*** Before taking this training you need to complete the Resource topic training.
I/ Business Example
In this example, we look at the company OC WoodTrend that produces custom wooden doors and windows.
OC WoodTrend produce decorative wooden doors and windows.
Each of these items are manufactured from several component items and use resources to produce them.
The list of items and resources needed to produce the finished product is recorded in the Bill of Material.
In addition OC WoodTrend sell different kits of build-it-yourself furniture. These kits are composed of precut wooden plates, screws and hinges. Each kit will have a Bill of Materials even though it is not used in the manufacturing process.
II/ Bill of Material Example 1
Let us try to understand the Bill of Materials concept by using the following example:
In order to manufacture an engraved wooden door we need two items: a plain wooden door and a handle.
In addition, we need to engrave a decoration pattern. To do that we need two resources: a lathe machine and a machine operator employee.
These items and resources combine the decorative wooden door Bill of Materials.
When starting the production process, this Bill of Materials is copied into a Production Order.
In real life production, Bill of Materials often have several levels. In our example, the wooden door component can also be a Bill of Materials
Note that the finished goods are also defined as items (Master data) in the system.
III/ Bill of Material Example 2
A Bill of Material may have several levels. A component item may be a also a produced item of another Bill of Materials. In our example, the wooden door is a produced item of a second level of Bill of Materials that has two items and one resource.
To start a production process, this Bill of Materials is copied to a Production Order.
We will further discuss the Production Order in the Production Process Course topic.
IV/ Bill of Material
1/ Example
Production -> Bill of Materials
This is how the Decorative Wooden Door Bill of Materials looks like in the system.
We can see that the decorative door is combined of:
- 1 Wooden door,
- 1 handle,
- A total of 3 cycles of the Lathe Machine
And 1 Machine Operator hour.
In WoodTrend, warehouse 02 was defined as the shop floor area and it is indicated in the document rows.
When created this Bill of Materials, the production management added a text row (number 4) indicating production instructions to rotate the door 180 degrees.
We can also see that the Lathe Machine appears in two rows. In row number 3 the machine is activated for 2 cycles. Then, there is an instruction to rotate the door and only after that the machine is activated for another cycle.
We can also choose the arrow buttons on the right hand of the window in order to change the order of the rows in the Bill of Materials.
At the bottom of the window we can define the product price manually or generate it automatically according to the components prices, taken from the selected price list, and resource cost.
2/ Pricing
Let us talk briefly about the bill of materials pricing.
In the unit price column, since this is a production bill of materials, we see the cost of each component. In a non-perpetual system the unit price is the price of the item, taken from the price list.
The Product Price, indicated at the bottom of the Bill of Material, can derive from the total components unit price (multiply by row quantity). To copy the total unit price, we choose the arrow facing down, as indicated in the image.
Alternatively, the product price can be entered manually.
By adding or updating the Bill of Materials, the product price is updated in the price list mention at the header of the Bill of Materials.
SAP Business One also provides a global update for a batch of Bill of Materials Product Price, according to the components prices. This is done in Production -> Update Item Prices Globally window.
3/ Phantom Item
A phantom item is a sub-assembly in the Bill of Materials that does not actually exist in inventory. It is used to simplify the Bill of Materials. Although the phantom item appears in the Bill of Materials, the Production Order will show the components needed to make the phantom item rather than the phantom item itself.
An item can be defined as a phantom item in the Item Master Data.
When copying the Bill of Materials to the Production Order, the phantom Bill of Materials components will be copied as well.
In the graphics we see a Skateboard Bill of Materials. The 4 wheels of the Skateboard are a phantom item. When the Skateboard Bill of Materials will be copied into the Production Order, the components: tire, rim, and screws will appear, but not the wheels.
The Bill of Materials requirements, of different departments, in the same company, can be different. The engineering department could create a multi level Bill of Materials to define an engine .The manufacturing department could then include this Bill of Materials as a single phantom item.
4/ Types
In the Bill of Materials (BOM) window you can choose one of four different types of BOMs.
We have already got to know the Production BOM so let us have a look at the other three types: Sales, Assembly and Template BOMs.
All these three BOM types are used in marketing documents and do not go through a production process (therefor, no resources are involved in these BOMs). The components of these BOMs are assembled to create the parent item.
The Sales BOM is used in sales documents. The parent item must be a sales item. For example, OC WoodTrend sell build-it-yourself furniture kits. The produced item is the kit name, and the component items are the inventory items that compose the kit. Once you select the parent item in a sales document, all the components appear as sub-items. You can update the quantities of the produced item or the components. However you cannot delete a component or add new sub-items to the kit in the sales document. When you set up the BOM, you can select the Hide BOM Components in Printout option, so that when you print the document, only the parent appears.
The Assembly BOM is similar to the sales BOM. It represents a collection of individual items in a set with a specific price. Unlike the sales bill of materials, only the finished product appears in the sales order document; the components do not appear as sub-items.
For both the sales BOM and the assembly BOM, you do not manage the finished product as an inventory item, but rather as a sales item. The components can be sales items and inventory items at the same time.
The Template BOM has no restrictions. Both the parent and the children can be any type of items. It can be used in sales and purchasing document. Once you select the parent item, all its children appear. You can delete, add or duplicate rows and make any modification as necessary inside the marketing documents.
V/ Category of the Item Master Record of the Produced Item in Bills of Material
Depending on the BOM Type you must define a certain category in the item master record of the produced item:
For the assembly and sales BOMs the finished product has to be a Sales Item.
Templates can have each of the three attributes (Purchased, Sales, and Inventory Items).
The finished product of the production BOM has to be an Inventory Item. If you also want to purchase this item, you can define it as a Purchased Item. If you also want to sell it, you should also define it as a Sales Item. If you produce it for inventory, as a component of another BOM, then do not define it as a sales item so it will not appear as a choice in a sales document list of items.
The components can also have each of the three categories (Purchased, Sales, and Inventory Items), and can also be purchased or sold individually.
The components for Sales BOMs and Assembly BOMs must be sales items.
VI/ Bill of Materials - Component Management
The Components Management window allows mass changes in multiple existing bills of material simultaneously.
You can:
- Add new components to selected bills of material,
- Delete specific components from selected bills of material,
- Change parameters (such as quantity, warehouse, issue method, etc.) for selected bill of material components,
- And replace bill of material components.
VII/ Summary
Here are some key points to take away:
- A production bill of material is a list of items and possibly resources that are consumed in the production process.
- A BOM may have several level, in this case one or more of the item components will also be a BOM.
- The production BOM can also list the order of using the different components and even add text rows with instructions.
- The Bill of Materials Component Management window allows you to perform changes for multiple BOMs simultaneously.
- In addition the production BOM there are three other types of Bill of materials that are available to use in marketing document: Sale, Assembly and Template BOMs.