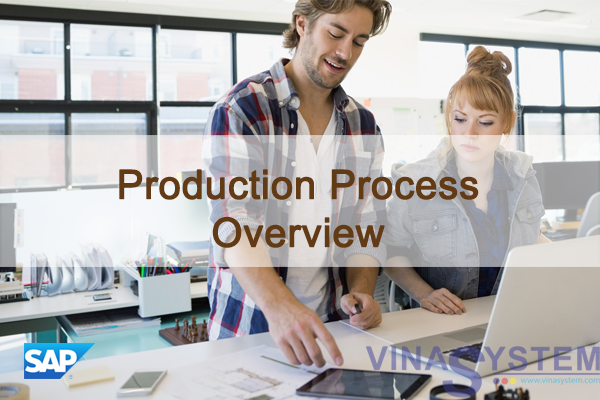
Tài liệu quy trình sản xuất trong SAP Business One - Production Process
Welcome to the Production Process training topic in SAP Business One.
In order to take this course, you should first complete the Bill Of Materials training topic.
After completing this topic, you will be able to:
- Add a Production Order
- Run a Production Process in the system
- Describe the inventory changes of item during production
I/ Concept
1/ Production Process
The production process starts with creating a Production Order. This is the main document in the production process. It records the progress of the production process for each item produced.
Before work can be done, the Production Order Status should be changed to Released. At this point, the Production Ordercan begin collecting the costs of production.
Components used in the production process can then be released to the shop floor (depending on the issuing method).
When all work is done, you report completion of the production order. At this point, the finished items are received into the warehouse.
Note that when an automatic method is defined for issuing the components to the shop floor, the timing of issuing the components and resources is when reporting completion.
When the production process is over, the Production Order should be closed. This closure creates a journal entry for balancing inventory accounts in a perpetual inventory managed companies.
Let us have a closer look at the Production Order and the production process in the next pictures.
2/ Production Order
A Production Order is a command to produce (or repair) a production item.
A Bill of Material (BOM) is copied into the Production Order document, then, the needed quantity of the finished good is entered and the desired due date of production along with other relevant data.
The Production Order also tracks all the material transactions and costs that are involved in the production process.
Note that production orders can be generated in the MRP and Pick and Pack processes as well. These topic are covered in details in the MRP and Pick and Pack course topics.
II/ Production Order
This is how a Production Order for the Decorative Wooden Door BOM looks in the system.
Once we choose the produced item in the Products No. field, the data is copied from the Bill of materials document to the Production Order.
At the header of the document, in the Planned Quantity field, we indicated that we want to produce 6 Decorative Wooden Doors.
When opening a Production Order the status of the order is set to Planned. In this status, you cannot issue components or report completion of the Production Order. However, you can make changes to the data in the Production Order. In order to proceed to the next step in the production process, the production manager changes the status to Released.
Production Order Dates
There are three important date fields in the header of the Production Order:
- Order Date – This is the date the Production Order was posted.
- Start date - This is the planned dated to start the production.
- Due Date – This is the planned due date of production.
The Start Date provides flexibility for the production manager in defining a sequence of schedule for the production orders.
We can see date fields in the rows as well. By default, The Start Date and End Dates in the rows are copied from the Start Date and Due Date in the header respectively.
These dates allow the project manager to define a sequence and a time schedule for the different phases of production, by changing the dates in the rows.
The arrows on the right hand of the window provide even more flexibility in defining the sequence of the rows.
III/ Create a Production Order and Release It
Let us start the production process for the Decorative Wooden Door.
Once the Production Order is entered, the following happens:
- The quantity of the item components of the Production Order were subtracted from the Available quantity of the items and became a Committed quantity (We can see it in the Item Master Data -> Inventory tab).
- The capacity of the resources of the Production Order was subtracted from the Internal Capacity and became a Committed Capacity (More about resource capacity in the Resource Capacity course topic).
The production manager changes the status to Released to start the production process.
Once the status has been set to Released, we can:
- Issue components (depending on the issue method),
- Receive the produced item into inventory and
- Report completion for a Production Order.
You still have the option to add or change components and resources that have not yet been issued.
Since WoodTrend manages the shop floor area as a separate warehouse, the production manager transfers the components from the main warehouse to the shop floor. He does that by creating an Inventory transfer from the context menu of the Production Order.
IV/ Issue Components and Issue Methods
The Issue for Production document subtracts the components from inventory and changes the capacity of the resource from Committed to Consumed.
Component items and resources can be issued using either the Manual or the Backflush method. The default issue method is defined in the master data of the item and resource. Then, this default is copied to the Bill of Materials document and can be changed by the row level. When the Bill of Material document is copied to the Production Order, the Issue Method in the rows is copied but can be changed again.
With the Backflush method – once the Production Order is reported as Completed, SAP Business One automatically issues the needed component items.
With the Manual method – the items and resources are not automatically issued. This enables you to post components issued to a production order precisely when they are required in the production process and also issue a partial quantity if needed, even before reporting completion.
Choose the context menu of the document to add an Issue for Production document. Alternatively go to Production -> Issue for Production.
Note: Items that are managed with serial numbers or batch numbers cannot be backflushed; therefore, they are automatically set to a manual issue method.
V/ Report Completion
At the end of the process, you report completion of production. This will receive the finished item into inventory and calculate the cost of producing the item.
Use the context menu to choose Report Completion.
When reporting completion, the system automatically:
- Receives the finished product into inventory by adding a Receipt from Production document.
- Issues backflushed components by adding an Issue for Production document.
- Calculates the cost of producing the item.
Note: a Receipt from Production document can be issued also from the Production menu entry.
VI/ Stock Changes for Standard Production Order
This slide summarizes the change made in the inventory data during the production process. In the Production Order, components are issued out of inventory. When the Production Order is completed, the finished product is received into inventory.
VII/ Summary
Here are some key points to take away from this session:
- The Production Order is based on the Bill of Materials.
- A production order is in a planning state until the status changes to Released. When the production order is released to the shop floor, items and resources can be issued to the production order and work can begin.
- Items and resources are issued when adding an Issue for Production document.
- Component items and resources can be issued using either the Manual or the Backflush method.
- With the Backflush method, once the Production Order is reported as Completed, the items are automatically issued for production.
- The manual issue method allows you to issue the components precisely when they are required in the production process and also issue a partial quantity, even before reporting completion
- When you report completion, the system automatically receives the finished product into inventory and issues backflushed components.