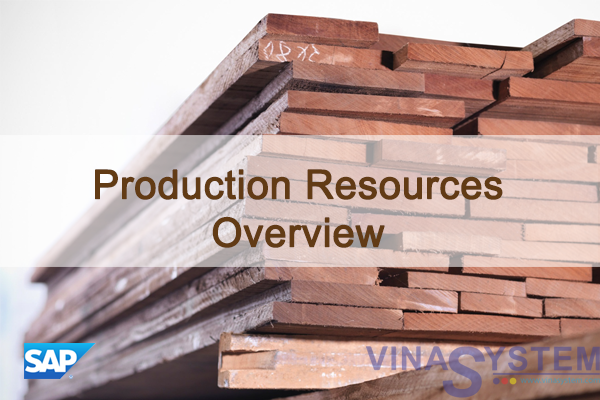
Tài liệu nguồn lực của quá trình sản xuất trong SAP B1 - Production Resources
After completing this topic, you will be able to:
- Explain the Resource role in a Bill of Materials and in the production process
- Create a Resource Master Data
- Define Resource Unit of Measure and run time
*** Please note that the pre-requisite for this topic is to be familiar with the topic Production Concept.
I/ Business Scenario - Manage and Plan Resources
In this example, we look at the company OC WoodTrend that produces custom wooden doors and windows based on customer specifications.
In order to manufacture these products, OC WoodTrend defined their employees and machinery as resources in the system. Now, they can manage their availability and capacity for the production process.
II/ Resource Concept
The Resource is defined as a master data in the system. There are three types of resources:
- Machine type – This is a resource that can be linked to one or more fixed assets taken from the Fixed Assets Master Data list, and
- Labor type - This is a resource that can be linked to one or more employee taken from the Employees Master Data list.
- Other Type – Any other resource that is used for production but is not a machine or labor.
When a Bill of Materials is produced, a machine is often needed in a production process and an employee may be needed as well, for example, to operate this machine.
In SAP Business One, we can plan and define a daily capacity for the resources. By monitoring this capacity, we can optimize the production plan and avoid bottlenecks.
1/ Resource Master Data – Header Information
The Resource Master Data can be found on the menu path Resources > Resource Master Data.
Resources are categorized by type and group. Each resource type can have a number of resource groups. The resource groups are used to group together machines, employees or other resources used in production that have similar types of costs.
Here we see a turning machine that is used in producing OC WoodTrend’s wood products.
Each resource has a defined unit of measure which will be used to manage scheduling and calculate costs during production. This machine unit of measure is Hour.
Each resource can have up to ten std. cost components. The amount entered in the Default Std. Cost column set the ratio of expense amount of each cost component in a journal entry made for the resource.
More information about cost calculation will be provided in the course Units: Production Std. Cost and The Accounting of Production.
2/ Resource Types
There are three predefined types of resources: Machine, Labor and Other. You can select the relevant type in the Resource Type field in the header of the Resource Master Data.
- When selecting Machine as the Resource Type, the Fixed Assets tab is activated in the master data record. One or more fixed assets can be selected for a machine.
- When selecting Labor as the Resource Type, the Employees tab is activated (instead of the Fixed Assets tab) and you can select associate employees with this resource.
- Other type is used for resources that are not fixed assets or employees.
Note that in order to work with fixed assets and see the Fixed Assets tab , you first need to activate this feature in the Company Details window in the Administration -> System initialization menu path.
3/ Resource Groups
The resource groups are used to group together machines, employees or other resources used in production that have similar types of costs.
In the Resource Group you connect the relevant resource type. Than, you can set up the standard resource cost components for that group. You can define up to 10 user-defined cost components. The name of each cost component is defined on the Resource Group level.
These values are the default cost components however they can also be changed by the resource level.
In our business example, OC WoodTrends has five lathe machines that they use in production. Since they have similar types of costs they have been grouped together in the same resource group.
More about production cost, G/L account determination for production and Production Std. Cost in the next course topics.
III/ Unit of Measure and Run Time
Capacity for a resource is measured in the resource units of measure. This unit of measure can be in time type units, like hours or minutes, but it can also be any other type of unit, such as a cycle, turn and so on. This resource unit is used when planning and consuming the capacity in Bills of Materials and in Production Orders, including all related transactions, such as the Issue for Production.
In order to translate the production quantity into time, we need to define the specific time period it represents. This is defined in the Time per Resource Units field that represents the time needed for the Res. Units per Time Period to be produced.
Example of Run Time Calculation
Let us examine this scenario: The resource usually runs in 15 minute cycles. The Unit of Measure for this resource is Cycle. The capacity of the resource is measured in Cycles and the quantities in the Bill of Materials are also in Cycles.
In the Bill of Materials we define that to produce 1 final product we need 3 cycles of this resource.
In order to define the run time of this resource in a specific Production Order we need to convert Cycle units of measure into time. The definition of the conversion between the resource unit of measure (Cycle) and time is as follow:
When the Time per Resource Units is 15 minutes, the Resource Units per Time Period equals to 1 cycle.
When the Time per Resource Units is 1 hour the Resource Units per Time Period equals to 4 Cycles.
This settings allows us to calculate the run time of the specific resource needed to produce required quantity of the final product. In our case, 3 cycles of this resource are needed to produce 1 final product. The resource run time calculation for producing 1 final product is as follow: the bill of material quantity X (Time per Resource Units / Resource Units per Time Period). In our example it is 45 minutes.
Now that we know the run time of the resource we can plan and manage capacity of resources. This will be described in the next course topic: Resource Capacity.
IV/ Production Order Run Time
Because different types of resources (Machine/Labor/Other) can be included in one Production Order, simplified calculation of the total production order run time is applied. The Total Run Time of a Production Order is the maximum value of the run time of each resources in the Production Order.
The run time of the specific resource is an estimated time required for the production elapsed run time and is calculated as follow:
(Parent planned Qty x base Qty) x the Time Per Resource Units / Resource Units Per Time Period values.
V/ Resource Account Determination
We already saw that the Resource Master Data inherits the cost component names and cost ratio from the Resource Group. Each cost component is related to a certain account in the GL Account Determination window (when using standard G/L account determination). There, we can define up to ten resource expense accounts, respectively to the ten cost components in the Resource Master Data.
The cost component in each row in the Resource Master Data is linked by the component number to the cost expense fields in the G/L account definition. In OC WoodTrens, Resource Std Cost 1 of the Lathe machine is named Amortization. However, the name of Resource Std Cost 1 in a Cutting machine is Lease. Both components are linked to the same Standard Cost Expense 1 and therefore both refer to account 510160 as shown in the image.
Resource Account Definition in Advanced Account Determination
If you have a need for a more complex mapping of cost components to accounts, then you need to use the Advanced G/L Account Determination rules.
To assign different accounts for different Resource Groups or even for a specific resource or a warehouse, use the Advanced G/L Accounts Determination Rules.
The first step is to select and activate a Determination Criteria for the resources. Use the menu path in Administration > Setup > Financials > G/L Account Determination > Determination Criteria – Resources.
Then, by defining the relevant rule in the Advanced G/L Accounts Determination Rules – Resources window, the required G/L accounts can be assigned to relevant cost components.
VI/ Summary
Here are some key points to take away from this session.
- There are two three types of resources: Labor, Machine and Other.
- The Machine resource type can be linked to a fixed asset in the system
- The Labor resource type can be linked to an employee in the system
- Each resource can have up to 10 cost components. Default cost can be defined in the resource group.
- Run time parameters should be defined in the Resources Master Data in order to plan capacity for the resource.
- Each resource component is related to a resource expense account.