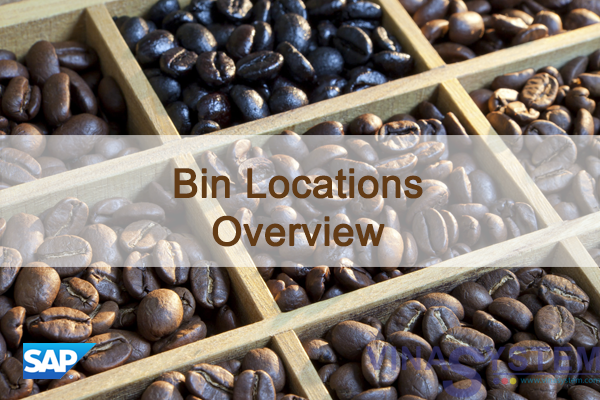
Bin Locations in SAP Business One - Bin Locations Overview
Welcome to the Bin Locations Overview course topic. This course is part of a series of courses available for the bin locations topic and presents a high level overview. Detailed information will be provided in all other courses.
At the end of this topic, you will be able to:
List the benefits of using bin locations
Describe at a high level:
- Bin locations set up process
- Manual and automatic allocation processes
- Reporting for bin locations
- The impact on the inventory taking process
I/ Business example and solution benefits
We start by introducing a business example and benefits of using bin locations
1/ Business Scenario
- You are working with George, the warehouse manager at OEC Computers, to analyze their logistics procedures and needs.
- He would like to improve the speed of the logistics process.
- Often a worker cannot quickly locate a specific item for picking.
- In addition, when receiving goods in the warehouse, another quantity of the same item may be stored in a different area of the warehouse. Because there is no record of where items should be stored, items are often stored in any vacant location.
- Furthermore, all of this leads to confusion and mistakes in the quarterly inventory count.
- You recommend to use the bin location solution for his warehouses.
a) OEC Computers Warehouse Structure (1/2)
Here is the structure of the OEC Computers’ New York warehouse.
This warehouse has 3 floors.
Each Floor is divided into Areas: Blue, Yellow, Green and Red.
b) OEC Computers Warehouse Structure (2/2)
Each Area is divided into Rows: 1 to 30.
Each Row is divided into Shelves: A to Z.
In the next slides we will see how the bin location solution can be used in OEC Computers’ warehouse.
But first, let us go over the solution benefits.
2/ Solution benefits
The Bin Location solution introduced in release 9.0 was designed to help SAP Business One customers to efficiently manage their warehouses and inventory processes
The SAP Business One Bin Location solution has many advantages:
- Significantly reduces picking time
- Facilitates & supports different picking requirements and processes
- Real-time inventory position helps enterprises to make better decisions
- Enhanced Warehouse reporting that provides benchmark information for KPI setting
- Faster and more accurate inventory counts
- Users can work in the system while bin locations are in set up
- Automatic processes allow:
- Quick processing of bin locations based transactions.
- Inventory storage/picking optimization.
- Minimize potential user mistakes.
- Automatic allocation of Serial Numbers and Batches managed items.
II/ Warehouse Sublevels and bin locations structure
We will now discuss the bin location managed warehouse structure
We will view the bin location code formed according to this structure
And then we will see the bin location set up process
1/ Warehouse Sublevels Structure
Bin Location Code Composition - Example
Let us get to know the bin locations managed warehouse Sublevel structure in order to understand how to define bin locations in OEC Computers warehouse.
A warehouse structure often consists of a combination of different levels such as an aisle, a shelf or a floor.
One area type can be a sublevel area of another type.
In OEC Computers, for example, a Shelf is a sublevel of a Row.
This means a Row contains several shelves.
SAP Business One supports up to 4 Warehouse Sublevels.
A combination of the Warehouse code and Warehouse Sublevels codes defines the unique bin location code.
An example in the graphic can be a bin location code 01-F1-RED-R01-B.
The same Warehouse Sublevel code can be used in many bin location codes.
We can see that Row sublevel R01 is connected to the Red Warehouse Sublevel and the Green Sublevel.
Floor sublevel F1, however, is connected only once to the warehouse and appears in only one combination of a bin location code.
***Note
- In small-medium warehouses we will probably choose to define less than 4 Warehouse Sublevels.
- For example, a Warehouse that consists of two Warehouse Sublevels: Rows and Shelves.
2/ OEC Computers Bin Location Code Structure
Now, let us see an example of a bin location code that exists in OEC Computers which is combined from all the Warehouse Sublevels mentioned before.
We can see that the bin location code is combined from the Warehouse and Warehouse Sublevels codes
3/ Bin Location Master Data
Each bin location has one Bin Location Master Data record.
The Bin Locations Master Data window is found under the Inventory à Bin Locations menu entry.
As in any Master Data window, in the Bin Location Master Data, a bin location code can be created updated, removed or duplicated.
The Bin Location Master Data window allows a creation of bin locations manually one by one.
There is also a separate management window that allows automatic creation of multiple bin location codes.
The Bin Location Master Data window can be divided into 4 logical parts: code structure, bin location properties, Restrictions on bin locations and bin location Attributes.
4/ Set Up Process
The diagram describes the workflow of the bin location set up process.
This set up is done in four phases:
In phase one we activate and set up a bin location managed Warehouse.
- The Bin Locations solution is enabled on a warehouse by warehouse basis in the Warehouse Setup window.
- In this window we also define the automatic allocation rules.
In phase two we set up Warehouse Sublevels and Attributes.
- Warehouse Sublevel codes can be defined manually one by one or a group of codes automatically.
- An Attribute is a characteristic, given by the user, that provides additional information or meaning to the bin location.
- After activating Attribute fields, they are added as filtering fields to the selection criteria of the bin location reports and their values are displayed in the reports output.
- They also appear as information fields in different windows in the Inventory module.
In phase three we set up the bin location codes and the Receiving bin locations.
- The bin location code can be generated updated or deleted one by one in the Bin Location Master data window.
- A management window also exists for automatically adding, deleting and updating a group of bin location codes.
- The Receiving bin location can optionally be used as a special section in the warehouse which typically represents a receiving inspection area or just a transit area for temporary storage of incoming goods.
In phase four we can define an automatic allocation strategy.
- These strategies set the bin locations for incoming bin location transactions.
- When creating a new document, the item in the row is automatically allocated in the bin location set by these strategies.
***Note: The Bin Location feature can be activated and set up in either a new or an existing company without interfering with the regular course of work.
III/ Business process integrated with bin locations
Next we will follow a simple business scenario starting with receiving goods to the warehouse and finishing by selling the goods.
1/ Business Process Integrated With Bin Locations
In the next picture we will follow an example of a business process that includes purchasing, transferring, picking and selling an item in a bin location managed warehouse that can be implemented in OEC Computers.
- We will start by adding a Goods Receipt PO to a special receiving area where inspection is made.
- Then, we will create an Inventory Transfer to move goods received to their storage bin location.
- After that, we will have a look at the inventory reports to view the transactions made and inventory level for each bin location.
- We will then review the delivery process of the item and focus on the Pick and Pack procedure.
- And finally we will add a Delivery document that creates an outgoing allocation from the item’s bin location.
- We will also see what happens when working with Serial Numbers.
While walking through this process we will review manual and automatic allocations.
2/ Allocations in Goods Receipt PO
OEC Computers purchases USB mouse units directly from the manufacturer.
The purchasing manager issues a Purchase Order and when the goods arrive at the New York warehouse the warehouse worker issues a Goods Receipt PO.
This Goods Receipt PO is the first step in our process.
Every inventory receiving document that involves a bin location managed warehouse requires allocation to specific bin locations.
This allocation can be manual or automatic.
The allocation is made per document row.
In order to manually allocate the quantity in the row, we choose the link arrow in the Bin location allocation field.
The Bin Location Allocation – Receipt window opens for this row.
In the matrix at the bottom of the window, we allocate the row quantity to the desired bin locations.
You may split the allocated quantity across multiple bin location codes.
For example when there is not enough room for all received units in one bin location, we can choose to allocate part of the quantity in another bin location.
3/ Automatic Incoming Allocations
a) Receiving Bin Locations
The items were allocated manually in the Goods Receipt PO, but the system can allocate these items automatically according to the definitions made in the Warehouse Setup window.
OEC Computers has a special receiving area in the New York warehouse.
This area is defined as one or more bin locations called Receiving bin location.
The Receiving bin location is a transit bin location that is used as an inspection area for quality check or any other receipt procedures.
When working with Receiving bin locations, all incoming transactions are placed in the Receiving bin locations unless alternative bin locations are chosen manually.
After completing the receipt, the items received can be transferred, using an Inventory Transfer document, to a storage bin locations.
b) Automatic allocation strategies
The second type of automatic allocation used for incoming inventory transactions is the automatic allocation strategies.
The bin locations set by these strategies, in contrast to those used by the Receiving bin location functionality, are typically the storage bin locations and not temporary bin locations.
One of the automatic allocation strategies is the Default bin location. You can define the Default bin location at the Warehouse, Item Group and Item level.
When you use the Default bin location strategy, the system will automatically assign the default bin location at the document row level. The system chooses the first default bin location it finds, starting with the Item level, then the Item Group, and lastly the Warehouse default.
In addition to the Default bin location, there are three other automatic allocation strategies. These strategies allow you to automatically allocate goods to the current, last, or any historic bin location where the item was stored.
4/ Changes in the Inventory Posting List
We can now view the inventory transaction made by the Goods Receipt PO in the Inventory Posting List.
The Inventory Posting List also reflects bin location transactions.
We can see the associated bin location for each inventory transaction.
You can choose to display the report per transaction or per bin location, per transaction.
You can also split transactions by Serial Numbered or Batched-managed items when working with Serial Numbers and Batches managed items.
5/ Bin Location Reports
George wants to see how many USB mouse items are left in the Receiving bin locations and then transfer them to their storage bin location.
He generates a Bin Location Content List report.
Two bin location reports were introduced in 9.0 version: Bin Location List and Bin Location Content List.
The Bin Location List displays a list of bin locations along with a variety of information fields for each bin location such as Warehouse Sublevels, Attributes and so on.
The Bin Location Content List report displays quantity balance per bin location per item.
Both reports allow certain functions to be performed directly:
- You can generate other inventory reports filtered by the selected bin locations.
- You can create an Inventory Transfer involving the bin locations selected, by choosing the Inventory Transfer button.
- And you can also set selected bin locations as defaults, directly from the report.
George Chooses the USB Mouse rows in the Bin Location Content List report and chooses the Inventory Transfer button and then Clear Bin Locations to issue an Inventory Transfer for this item.
6/ Allocation in Inventory Transfer
George wants to transfer the USB mouse items from the Receiving bin location to the storage bin location.
When George chooses the Clear option in the Bin Location Content List, an Inventory Transfer opens.
The Warehouse, bin locations and quantities are copied from the selected rows in the Bin Location Content List.
The Inventory Transfer document was adapted to handle inventory transfer between bin locations.
This transfer is also possible within one warehouse, from one bin location to another.
Look at the image, there are two bin location columns in the Contents table: From Bin Location and To Bin Location.
While the fields in the header hold the default values for the fields in the grid the values of the fields in the grid can be changed and the inventory transaction is made according to these values.
This enables the Inventory Transfer document to be created from multiple originating warehouses simultaneously.
This functionality is available even if the bin location functionality is not activated for any warehouse.
7/ Bin Locations in Pick and Pack
Michael, the sales manager issued a sales order for 25 USB Mouse items.
At this stage, no allocation is done.
George the warehouse manager starts with the Pick and Pack process in order to generate pick lists for his workers.
The Pick and Pack manager has been adapted to handle outgoing allocations for the Pick List.
In the Open drawer, choose the Release to Pick list button to enter the Pick List Generation Wizard.
In the first step you can filter the Warehouse Sublevels and Attributes of bin locations you want to pick from.
Then, in the second step, you can indicate if you want to create several pick lists by splitting the order rows by a Warehouse, Warehouse Sublevel or Attributes and also choose the automatic allocation method.
This automatic allocation method can be changed manually and is not necessarily the default method defined in the warehouse.
In the third step you can see and edit the list of the proposed Pick Lists about to be generated.
Choosing the Generate Button creates the Pick Lists that appear on screen.
8/ Pick List
In the Pick List we see one line per bin location per item per Sales Order line.
- Before items are picked, you can still re-allocate them.
- It is important to be able to reallocate directly from the Pick List as the picker may select items from different bin locations then the those specified in the Pick and pack Manager.
- In this way, the picker will not have to navigate back to the Released Pick and Pack screen.
A Pick List ordered by warehouse sublevels and bin locations enables a fast picking process.
George chooses the Create button to generate a Delivery for the Mouse USB item.
9/ Allocations in Delivery
Every inventory issuing document that involves a managed bin location warehouse requires allocation of items to issue from specific bin locations.
In our example, we created a Delivery document during the Pick and Pack process, containing the items and quantity picked.
Let us see how items are allocated when copying the Delivery from a Sales Order or when add it directly.
The Bin Location Allocation – Issue window structure is similar to the Bin Location Allocation – Receipt window.
In this window we can see a list of bin location codes with quantities available to allocate from.
You may allocate from any row with available quantities to allocate.
Enter the quantity you wish to allocate from any available bin location to combine the total.
In the image displayed we can see the Delivery document George created from the Pick List.
- George needs to issue a quantity of 25 from warehouse 01.
- There are three bin locations with positive quantity of the item in the row.
- George wants to empty the first bin locations in order to minimize the number of bin location for this item.
- He chooses 5 from the first bin location to empty it and another 20 from the second.
- Then, he used the CTRL+B keyboard combination to enter the remaining quantity to allocate.
You can perform an automatic allocation by choosing the Automatic Allocation button.
Note, the system can also perform automatic allocation when issuing goods.
Let us have a look at the different automatic issuing methods.
10/ Automatic Allocation Issuing Methods
George asked you if there is an automatic way to allocate first from the bin locations containing the minimum quantity.
You advise him to use the Ascending Quantity automatic method.
In the table displayed we see all issuing methods along with a short description.
In the Warehouse Setup window we choose one method as default for all outgoing transactions made in this warehouse.
However we can change the method per document or row level.
The Single Choice method allows the user to manually control allocation process when there is more then one allocation option
The Bin Location Code Order and the Alternative Sort Code Order methods enable automatic allocation according the coding representation of the bin location.
The Descending Quantity and Ascending Quantity methods enable automatic allocation according the quantity already allocated in the available bin locations.
With FIFO and LIFO methods items are allocated according to the order of the entrance date of the item in the bin location.
When the system automatically allocates the items, the bin location allocation column is populated automatically and we do not have to enter the Bin Location Allocation – Issue window.
We can however, enter the window to review the allocation made by the system and change the allocation manually if necessary.
11/ Allocation of a Serial Number or Batch managed items
In the allocation process of serial number or batches managed items we allocate quantities per serial number or batch.
Each serial number or batch has to be associated with a bin location.
You can enter the Bin Location Allocation window from the Bin Location column.
There are two methods of allocations with serial numbers and batches:
- The first method is to first pick the bin location and then, with in this bin location, the specific serials or batches.
- The second method is to first pick the specific serial or batch and then choose the bin location the specific item chosen is stored in.
In most cases, OEC Computers customers do not mind which serial number is attached to the items they purchase.
For this reason, the method normally used in OEC Computers is the first method - bin location first and then serial number.
IV/ Inventory Taking process in a bin location managed warehouse
Finally we will view the changes made in the Inventory taking process.
Bin Locations in Inventory Counting
The inventory counting process is also affected by the Bin Location solution.
In the Inventory Counting and Inventory Posting windows, the list of items is split by warehouse and bin location.
When adding items, a selection criteria window opens, enabling you to filter the counting list by Bin Locations.
V/ Summary
Here are some key points:
- List the benefits of the Bin Location module
- Generally describe the following:
- Bin locations set up process
- Manual and automatic allocation processes
- The bin location reports and changes made in the Inventory posting list report.
- The impact on the inventory taking process