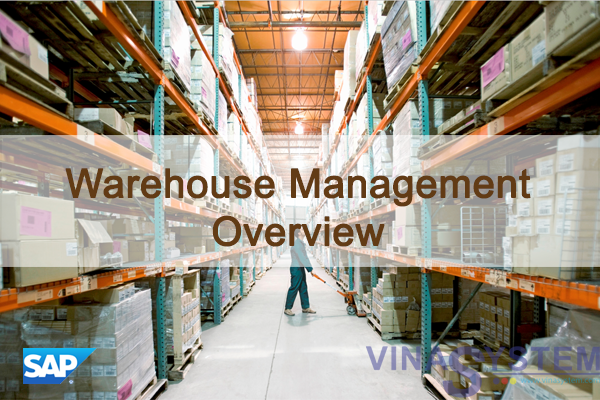
Warehouse Management in SAP Business One - Warehouse Management Overview
At the end of this topic, you will be able to:
- Create a warehouse
- View a warehouse’s bin location structure
- Describe the drop shipment process
Your company makes, buys and sells items that are stored in multiple warehouses.
One of the warehouses is controlled by bin locations.
Another of the warehouses is physically located at a vendor so it is represented as a drop ship warehouse.
Your business is growing in a new region, so you create a new regional warehouse to expand your distribution.
I/ Warehouse and Document
Documents in the sales and purchasing processes reference a warehouse whenever they contain items.
Inventory documents such as the goods receipt, inventory transfer and goods issue always reference a warehouse.
Because warehouses are so key in any process involving items, we will look at how warehouses are defined and what they signify.
1/ Warehouse
- A warehouse represents a location where goods are stored.
2/ Defining a Warehouse
- The first step in defining a warehouse is to enter a Warehouse code and a Warehouse name.
- Then you need to specify where the warehouse is by entering location information. This location information is important. because typically the address of the warehouse associated with the first document row is used as the ship-to address.
- Most warehouses are created for physically storing items, but a warehouse can also be set up as a virtual warehouse to manage business processes where goods are shipped directly to your customers from one of your vendors. We call this a drop ship warehouse. If you choose to set a warehouse as a drop ship warehouse, you will have the additional option to manage serial numbers and batches in the drop ship warehouse.
- Another option is whether you want this warehouse to be considered in material requirements planning.
- A third option, new in 9.0, is the option to use bin locations as sublevels within your warehouses. This option would not be available if this is a drop ship warehouse.
- Other fields for tax information may be visible depending on the localization.
II/ Bin Locations
1/ Bin Locations in the Warehouse
- One option to improve logistics of warehouse processes is to implement bin location management.
- Bin location management helps you keep track of the items in a warehouse down to the physical bins that store the items.
- Using bin location management can help you optimize storage space, quickly locate items, and plan out efficient routes for picking.
- In our business example, Warehouse 5 is managed with bin locations. The warehouse is broken out into 4 levels.
- The top level is the warehouse.
- Below the warehouse, the first sublevel is made of 4 aisles: A1 through A4.
- Each aisle is made up of 6 shelves S1 through S6, and each shelf as 3 levels.
- The bin location code is made up of the warehouse code plus each sublevel. Here we see the third level of shelf 1 on aisle 1 has a bin location code of 05-A1-S1-L3.
2/ Bin Locations in Business Processes
- Here is a quick glance of the main business processes showing steps in the process that include bin locations. Bin locations are available on all documents that have inventory movements.
III/ Drop Ship Process
- Sometimes, you have products you sell that you do not make or store. Instead, your company serves as a middleman between your customers and vendors. In those circumstances you can set up a drop ship warehouse.
- When a customer orders a product from a drop ship warehouse, the system opens the procurement confirmation wizard when you save the sales order.
- The wizard creates a purchase order for the preferred vendor of the item.
- The ship-to address in the purchase order is the ship-to address of the customer in the sales order.
- When the vendor receives the purchase order, they ship the product directly to the customer.
- The vendor invoices you for the cost of the product, and you invoice the customer for the sales amount.
- With the drop ship process, there is no effect on inventory quantities or values. No goods movements are posted. No journal entry is made to reflect inventory value changes. Therefore, the drop ship warehouse is not displayed on inventory reports.
- To set up a warehouse, mark the Drop Ship checkbox. If you would like to include the ability to track serial numbers or batches in a drop shipment, then also mark the Manage Serial Numbers and Batches checkbox.
IV/ Summary
Here are some key points:
- Warehouses are specified in all inventory documents and in any sales and purchasing document containing items.
- Bin location management can be used to optimize storage space, quickly location items and plan efficient routes for picking.
- A bin location code consists of the warehouse plus each sublevel.
- Bin locations can be specified on all documents that have inventory movements once bin location management is activated.
- You can set up a drop ship warehouse to represent a vendor’s location. Then when you save a sales order for that warehouse, then procurement wizard suggests a purchase order to the vendor. The items are sent directly to the customer. The vendor invoices you and you invoice the customer.